Advanced Manufacturing
Innovation in the aftermath of Covid-19: necessity is the mother of invention
The manufacture of millions of swabs in a short period of time, robots that help communicate with patients, and improved face masks for protection against the Coronavirus. These are the success stories of three Israeli industrial companies that identified the opportunity and, together with the support of the Israel Innovation Authority, developed innovative solutions for the challenges posed by Covid-19
At the very beginning of the Coronavirus pandemic outbreak in Israel, the Innovation Authority identified several immediate challenges that the country would need to find a solution for in order to contend with the virus. First, the shortage of medical products such as swabs needed for the Covid-19 test kits. These swabs are not produced in Israel and are difficult to obtain in a time of increasing global demand. The second challenge is the continued disruption of the supply chain due to the impaired import of raw materials that are only manufactured abroad and used by Israeli factories. A disruption in supply leads to a situation in which the industry can no longer continue operation and production. The third challenge, also related to the cessation of imports, is a national shortage of medications, baby food, and other basic products, some of which are produced overseas.
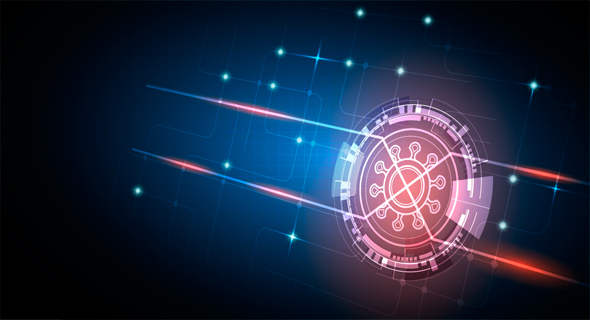
An innovative and creative approach has transformed these challenges into an opportunity for rapid growth for industrial companies in Israel. Following the Corona crisis, some companies have seized the opportunity and accelerated pilots for the development of advanced technological products. The Innovation Authority did not stand by idly during this period and was quick to offer support programs and financial grants to Israeli companies interested in joining the effort to confront these challenges. "With the outbreak of the pandemic, the Authority understood the potential for possible damage to local industry and with it, the new opportunities which had been created," says Ronit Eshel, Director of Strategy in the Innovation Authority's Advanced Manufacturing Division. "The State of Israel needed local production of medical products and basic consumer products. Companies that succeed in manufacturing the required products in a short period of time will fill their production capacity and safely navigate the crisis. We, therefore, published calls for proposals to companies to turn the crisis into opportunity and initiated contact with large numbers of industrialists. We were happy to find a positive and quick response to our call to advance technological developments that meet today's pressing needs. Within just one month, 75 factories submitted requests to develop a product or a process that will help cope with the crisis."
Israeli swabs
The shortage of swabs that constitute an integral part of the Covid-19 test kits was one of the first challenges identified with the outbreak of the pandemic in Israel. The parties responsible for procurement in the Ministry of Health and on the relevant Ministry of Defense committee approached the relevant companies to manufacture the kits' missing items. One of these companies was 3BY – a company located in the Tefen Industrial Park – that manufactures medical devices. The company accepted the challenge, identified the opportunity in manufacturing the swabs, and initiated a process of rapid development and production. Within three months, 3BY had progressed to producing millions of swabs.
The company, which until then manufactured medical products using injection technologies, is led by Alejandro Wolanski, the CEO, and Rafi Alchek, its VP Operations. "In March 2020, we received a call from the Ministry of Health and the National Security Council to help with the creation of the famous swabs for Coronavirus test kits. Until then, the swabs had been imported from overseas because not a single Israeli company produced them locally," Wolanski explains. "Thanks to our expertise and production capabilities that were suitable for manufacturing the swabs, we entered into a joint development project together with the Ministry of Health and the IDF Technology Corps. We then responded to a call for proposals published by the Innovation Authority and submitted a plan for producing the swabs in Israel, with help from England. Our proposal was accepted and in less than a month we established an automated production line that supplies 60 thousand swab kits every day."
Long-standing proficiency with new development processes
The 3BY leaders' first encounter with the swab required for the test was only as they were beginning the project. "Within five days we successfully developed a mold for producing the plastic swab stick. The complicated part was how to attach absorbent material, made from either nylon or Dacron fibers of exactly the right size to the head of the swab stick. This material must be able to absorb the correct level of a collected specimen. We achieved this by a process from the textile industry called flocking. Tests conducted by the Ministry of Health on confirmed Coronavirus patients revealed that our swab is high-quality and efficient, and we received the necessary approval to proceed with the manufacturing," Wolanski describes.
Wolanski and Alchek explain that the company's innovation and development was achieved specifically during the pandemic because of its success in developing innovative processes and connecting them to production capabilities from the plastic industry. "We adapted in record time to produce the swabs and this more than filled our production capacity."
3BY is located in the scenic and green Tefen Industrial Park that provides employment for many families from Karmiel, Ma'alot, Nahariya, and the surrounding Druze villages. "I joined the industry following my IDF service in 1988, and I've been here ever since," Alchek explains. "In one of the factories, I stood next to Stef Wertheimer who imbued us with a spirit of Zionism that has remained with me ever since. It's important for me to pass down these values to the next generation and I'm always happy to employ young workers from the local area. Our goal now is to keep developing – to introduce new technologies, integrate robotics and computerized optic systems in quality control, and to create additional jobs for the local population."
An autonomous robot that helps the doctor and patient
RoboTiCan is another company that has succeeded in quickly adapting an initial product – one originally intended for a completely different purpose – and to provide a solution for a medical need created by the Coronavirus pandemic. This company, located in the Omer Industrial Park, supplies mobile autonomous robotic platforms. RoboTiCan was founded in 2013 and today employs 35 workers in different fields – mechanical, electrical, and software engineers. The R&D teams focus primarily on the development of large numbers of autonomous robotic products and are also participating in joint projects with the Ministry of Defense.
With the outbreak of the Coronavirus pandemic, RoboTiCan contacted the Soroka Medical Center and began a pilot with an autonomous robot that connects doctors and patients, measures patient indices, and even establishes virtual communication between them. This is all done autonomously so that the physician is not exposed to the patient or to the virus.
Hagai Balshai, the company's CEO and co-founder, says that because the company engages mainly in development, it was unaffected by the pandemic and did not need to cut back its personnel. "Nevertheless, we couldn't remain indifferent to the situation so we contacted Soroka to see if our robotic systems could help somehow in the battle against the virus. When they raised the important need for doctor-patient communication, despite the physical distance between them, we proposed using robotic platforms. They eagerly accepted the idea and the Innovation Authority agreed to help us with fast-track scrutiny and approval and with financing the study."
Diagnosis for a patient in a remote hospital
Towards the end of March, RoboTiCan had already begun work. "The robot's flexibility and its compatibility to the medical needs depended not only on the platform itself but also on our team who worked day and night for weeks to complete the task," Balshai describes. "During the first wave of Corona, the robots were directed at establishing doctor-patient contact and communication and at allowing the medical team spatial control of the patients. For example, when a team of physiotherapists was required to visit the Corona Department, only one of them actually entered the ward. With the help of the robot, the therapists who remained outside could observe the patients' condition, received instructions, and did their job. The robot enables them to function from a distance. It receives the feedback from the patient and enables the medical team to run the department in a smooth and optimal manner."
As far as the company is concerned, the next stage is for robotics to perform logistical tasks within the departments, thereby saving skilled, professional, and vital personnel for other tasks. "Together with the crisis, the Coronavirus also brought opportunities for a fast-track revolution in fields of therapy that help the patient from a distance," Balshai explains. "These capabilities can also be harnessed to treat other medical cases. For example, when a medical specialist from the center of the country is asked to make a diagnosis for a patient in a hospital located in the periphery or in a private clinic. The diagnosis can be made from a distance with the help of a robot and the doctor can continue providing optimal treatment to his own patients. As far as we are concerned, robotics has yet to fulfill its full potential."
Local Israeli manufacturers' right to exist
In 2013, when Sion Medical was founded from the merger of two Israeli industrial companies, Daniel Lev, the owner and deputy CEO, was surprised to discover that one of the companies he had acquired was Israel's sole manufacturer of bandage products. "At the time there were less than ten manufacturers of these products in all of Europe – and thousands of Chinese producers," Lev says. "In 2016 there were only three European manufacturers – the remainder had transferred their production to China. Our challenge was to prove our right to exist in a chaotic and price-oriented market despite the trend of moving to Chinese production. We did so via uncompromising service and quick supply of products that were made possible thanks to the large stock we always keep on hand. This strategy proved itself without a doubt during the Corona crisis. We also adopted an innovative approach and are constantly looking for ways to do things differently and change even the common products that have served us well for decades."
One of Sion Medical's developments is connected to the gauze used in orthoscopic surgery. For years, the gauze used in such operations had an interwoven identification thread that allows surgeons to easily locate it in the abdominal cavity and extract it at the end of the operation. The interwoven thread was caught with miniature tweezers, but the gauze wasn't always extracted with it. The technology developed by Sion Medical melds the thread into the gauze instead of weaving it. Another example of the company's innovation is the development of a unique dedicated product based on hydrogel and medical honey for treating infected cuts, mainly in deep chest surgery. This development was achieved with the support of the Innovation Authority after Sion Medical purchased Triticum, a Dutch company manufacturing and marketing medical honey products used in the treatment of severe skin problems – from burns, through hard-to-heal wounds, to cuts and skin rashes.
Israeli masks that speak Chinese
For many years, Sion Medical was a leading player in the field of personal protective equipment (PPE) for medical teams. "We are Israel's leading manufacturer of protective kits (gowns, masks, etc.) for operating theaters, where the aim is to shorten the waiting time between operations and reduce the potential for infection," says Lev.
"On January 15, when the first reports of the Corona pandemic were received, we realized that the situation could escalate, and we brought to Israel 2 million masks from our factory in Mexico. In February, I also submitted a working paper to the Ministry of Health about the establishment of production lines for masks in Israel. After we won the first Ministry of Health tender for setting up a production line for N95 masks, we also won a tender for the manufacture of surgical masks. That's when we began an intense effort began to bring the production machines to Israel. During March 2020, we ordered two production lines for N95 masks and eight more for three-layer masks," he concludes.
One important illustration of the mask production challenge that Sion Medical faced is that the machines arrived in Israel with operating instructions in Chinese but without a team of engineers or instructors to explain how to use them. "Our team worked around the clock to learn how to operate the machines and successfully produce high-quality masks," Lev explains. "When we understood that the Coronavirus is here to stay for a long time and that the need for masks will only increase, we decided to make our masks better, to differentiate them from those produced by competitors, and to create a comparative advantage over the existing market. We invested heavily in development to create a face mask that would protect from Covid-19 while also being comfortable to wear for long periods of time. Sion Medical's aspiration is to be a leader and groundbreaker in an industry that for decades underwent only minor changes. We can only achieve this innovation thanks to the excellent people who are loyal to the company's Zionist idea, to the company itself, and to society at large. This is the only explanation for how in less than a month, from the moment we received machines that "spoke Chinese", without engineers or an instruction manual, we began mass production of quality masks."
"This entire operation was undertaken with the immense support of the Ministry of Defense and the Department of Production and Procurement (DOPP) who realized the importance of preferring Israeli products. This support was only short-term and today the production lines stand idle as the government prefers to purchase cheap Chinese face masks instead of those produced locally."
This is also the place to mention the Innovation Authority that has supported us out of an understanding that innovation exists even in a traditional industry and that the old and simple products are often the most important – just like the masks. The Innovation Authority also understands that these industries are precisely where there are places and a need for innovation", he emphasizes.
The article was written in collaboration with the Israel Innovation Authority, responsible for the country’s innovation policy. Its role is to nurture and develop Israeli innovation resources, while creating and strengthening the infrastructure and framework needed to support the entire knowledge industry.
Part One: The Cutting Edge: Manufacturing using advanced technologies
Part Two: A fast-track to innovation: The R&D Preparatory Incentive Program
Part Four: Smart industry and advanced mechanization: a technological leap forward to the global market
Part Five: Creating a future: sustaining the environment