Advanced Manufacturing
Creating a future: Sustaining the environment
A chair and car made of waste, food trays from recycled raw materials, and nutritious and tasty, vegetarian milk-product substitutes. With the support of the Innovation Authority, three Israeli companies are developing innovative manufacturing processes and striving to realize the ecological vision
Try and imagine a cleaner world in which household waste becomes a valuable and eco-friendly resource. This is the vision of UBQ Materials, a cleantech startup that uses a revolutionary process to transform all home waste into a renewable resource. Unlike the recycling industry that requires sorting and separation of the different waste materials, with UBQ's process, the heterogeneous home waste is utilized in its entirety. All solid urban waste that is otherwise destined for disposal at a landfill – food waste, dirty cartons, mixed plastic and paper – becomes a new raw material called UBQ™ (a registered patent) – a renewable thermo-plastic material. Moreover, all the products to be manufactured with the new raw material can be repeatedly recycled into it again and again.
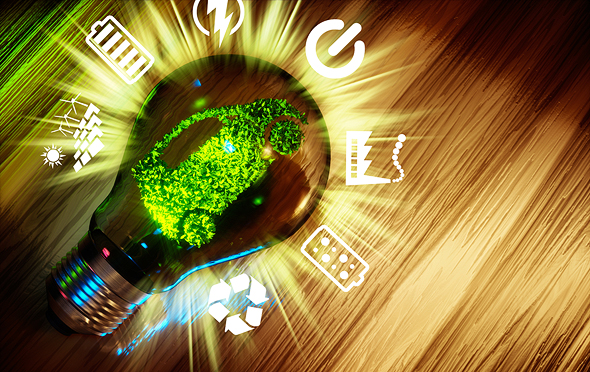
Transforming home waste into an industrial raw material
Jack (Tato) Bigio, co-founder and Israeli CEO of UBQ, fell in love with the idea of using an efficient process to transform home waste into a new and usable raw material for industry, thereby preventing waste from reaching landfills. "We founded the company in 2012 and began development of the technology," he says. The name UBQ is an abbreviation of the word ‘ubiquitous’ which means the ability to be everywhere at the same time. Waste is everywhere that people go – and the company's solution is suitable for manufacturing nearly any product application so that both the problem and the solution are ubiquitous.
"We developed the technology with the support of the Israel Innovation Authority," Bigio says. The technology is based on the idea that all organic components, whether chicken or cake remains, banana peel, or a paper carton, have a similar make up. The organic components naturally decompose into the basic materials from which they are made. In UBQ's process, these components are broken down and are subsequently blended into a uniform matrix. The non-organic plastic in the waste is melted down to become part of this matrix.
A green solution for the plastic industry
UBQ's development is conducted at the company's factory at Kibbutz Tze'elim in southern Israel which is already supplying UBQ™ to local manufacturers. The factory also boasts advanced laboratories that constitute the foundation for its R&D activity. The municipal garbage trucks offload at the UBQ factory instead of the Dudaim landfill site which is located a mere 20 minutes away. Machines in the factory identify and remove metals and glass from the household waste mixture, these abrasive elements are not used in the feedstock of UBQ™ and are instead transferred to conventional recycling processes. Via the unique UBQ process, the home waste is transformed into a material with plastic-like qualities – becoming a liquid when heated and solidifying when cooled and can therefore replace conventional plastic made from oil. "We have, in essence, invented a new material for the plastic industry, made entirely from waste," says Bigio.
"Today, the factory receives about 7,000 tons of home waste that then become approx. 5,000 tons of raw material which is sold to the plastic industry to manufacture products such as chairs, tables, hangers, plastic parts for the auto industry, and pipes. UBQ Material can be used as a raw material for any conventional plastic product. In practice, we are a green and cheaper alternative to the plastic industry," he explains.
In a world increasingly aware of the environmental damage caused by the plastic industry, it is no surprise that UBQ is turning out to be an attractive raw material. "We have won numerous global awards and have some mega-clients, including McDonald’s and Mercedes-Benz," Bigio says. "Today, we are closer to opening our first overseas factory, with the goal of achieving a yearly capacity of 70,000 tons of UBQ Material aimed at the European and North American market. Our vision is to become a top global player in the field of sustainable alternative materials. With the help of local collaborations, the company aspires to expand to global markets, increase the scope of production, and to realize the ecological vision – a world where waste is no longer wasted."
Growing demand for recycled raw materials
"About 350,000 tons of hazardous waste are created in Israel every year, in almost all recognized sectors of industry," says Dr. Ami Applebaum, Chief Scientist at the Ministry of Economy and Industry and Chairman of the Israel Innovation Authority. "The Innovation Authority plays an important role in the creation of technological solutions that contribute to improving the environment and to the transition to use of natural or recycled materials. The Authority encourages Israeli industry to advance R&D programs that will lead to economization of resources and a move to natural alternatives. The connection between startups and industry is essential in promoting a circular economy and green environment".
The increasing awareness regarding environmental sustainability and the damage caused by using plastic has led to a growth in demand for products made from recycled materials. "Alongside market demand, this issue has also been reinforced by regulation, primarily in Europe," says Natan Vilner, CEO of the veteran company MCP that specializes in the production of trays for the food industry. Vilner, who is also Chairman of the Plastics and Rubber Sector of the Israel Manufacturers Association, says that "from 2023 onwards, only food trays made with at least 35% recycled materials, that have already been used on the market, and that have undergone a repetitive process back into raw materials will be permitted for sale. In light of these requirements, we started to strive towards manufacture of plastic food trays that contain 80% recycled material. This decision drove us to develop an entire line of new products, a challenge for which we received grants from the Innovation Authority."
Although Vilner worked with the Innovation Authority in the past on various projects, this was MCP's first experience with the Authority. After receiving the necessary approval, the company embarked on the development process. The MCP factory at Kibbutz HaMa'apil manufactures trays from a material called CPET that enables heating and freezing in a microwave or regular oven, including those we are familiar with on airplanes.
Until now, MCP's innovation has been expressed primarily in its wide range of trays and production flexibility. The current need constituted a significant step-up for the company from a developmental perspective. "A process like this can be achieved via a technology that both shreds the raw material and restores it to a state where it can be reused for food," Vilner explains. "So far, we have only used shredded material in the factory's internal cycle or in new material. In this new situation, we had to check how other materials in the tray production process reacted in order to preserve its functionality and its suitability for use in both microwave and regular ovens. This is an extremely complex process that necessitated full technological development of a whole family of products."
Eco-friendly food trays
According to Vilner, sustainability and recycling are at the top of MCP's priorities and, to a large degree, are also dictated by the clients. The food companies realized that they needed to adapt to market needs and to regulation and to reduce their use of plastics while understanding that it was impossible to abolish the use of plastic trays altogether. "During the last two years, the MCP R&D team worked intensively on developing CPET trays that contain an average of 80% recycled material. These trays, named RePET, maximize the plastic's lifespan. The high demand for the recycled material significantly raises production costs – its price is currently almost double that of new raw material. Furthermore, we discovered that no factory in Israel has the knowledge and capability necessary to conduct this process and that the companies in need of this raw material struggle to obtain it. In most cases, importing is the simple solution but the Corona crisis has proved the indispensability of local industry. The almost complete cessation of international travel led to a large global shortage of food trays and, overnight, we applied our manufacturing capabilities to assisting different projects such as meals for the elderly, both in Israel and worldwide," he describes. "Although CPET is a somewhat niche industry, this development is revolutionary for us," Vilner explains. "We succeeded in manufacturing food trays with 75%-80% recycled material and the entire production process was conducted in an Israeli factory. The Innovation Authority's financial support enabled us to achieve this breakthrough and we are currently undertaking preliminary advertising of the RePET line of products. Development is still at its peak and we are yet to overcome all the challenges, but our vision is to be one of the world's leading manufacturing companies of these products."
Dairy alternatives from natural raw materials
Today's green and healthy trend has also pervaded the field of food-tech that seeks to provide a solution for an increasing number of consumers who wish to avoid or reduce their intake of milk and soy products. Yofix is a startup that develops and manufactures dairy alternatives based on purely natural plant-based materials. The company began in Strauss's incubator, 'The Kitchen', which is supported by the Innovation Authority. At the end of a 2-year development process, Yofix succeeded in producing the 'ONLY' brand that was already being sold in supermarkets – a unique, Dairy-free probiotic yogurt that contains vegan probiotic bacteria based on rich natural raw materials including oats, legumes, seeds, and fruit.
"The company develops and manufactures dairy alternatives from completely natural raw materials," explains Yofix’s CEO Steve Grun, who was born in Belgium and active in the food industry in Israel and Europe for more than 20 years. "The basic raw material of vegan products is usually soy but, in addition to still being perceived as a controversial ingredient, many people do not like its taste. Moreover, sometimes, as part of the process while working with soy, its water and dry material are extracted, and preservatives and other materials are added, thereby making the soy only a small part of the product."
The understanding that a consumer looking today for a milk substitute is not prepared to compromise its taste, nutritional values, and ingredients – led Ronen Lavee, Yofix's founder, to search for natural components that will enable the development of an entirely plant-based product. Lavee, who himself is lactose intolerant, is an agricultural mechanical engineer who worked for several years in Asia, where he began the production of plant-based milk and yogurts in his home kitchen. After returning to Israel and seeing the milk substitute products on offer at the time, he began looking for additional natural raw materials. He took oats, lentils, sesame, and coconut, fermented them at home with probiotic materials, and successfully created various flavors. He later produced unique nutritional combinations until reaching a stable product that needed no artificial additives at all. This gave rise to the 'ONLY' brand – a yogurt substitute made from simple ingredients available in every kitchen – oats, lentils, coconut, sesame, fruit, and sugar.
The delicacy of the future: A vegan substitute for a probiotic yogurt
Yofix conducted a pilot with the products and obtained investment from large corporations that identified the potential of using natural raw materials. "It is customary to use soy, almonds or cashew, and more recently, oats, when producing vegan products", says Grun. "Yofix also uses oats but adds lentils, sesame and coconut to them. These four ingredients are the base of our product, and each one of them contributes to its stability. The result is a tasty product with high nutritional value that also provides a sense of satiation".
Today, Yofix offers a probiotic spoon-eaten yogurt and a yogurt drink. "Working with the Innovation Authority helped us tremendously during the development process," explains Grun. "The Authority helped us contend with the existing regulation and bureaucracy in the food-tech industry and with developing the product's prototype. We first launched our product on the market two years ago and introduced a new brand in the UK called 'The Real Foodists'. This brand includes YO'RIDGE – a new and unique product range that is half yogurt and half a porridge/oatmeal that was developed and manufactured here."
In 2018, Yofix won the European innovation program for Food-tech startups run by PepsiCo – a multi-national American corporation that manufactures and markets food products and beverages – and received a grant of EUR 100,000. The reasons cited for the award were the product's strategic launch and the significant retail growth during the program. "We also participated in ANUGA – the largest global food fair held in Cologne, Germany, and were selected as one of the 50 most innovative companies from among 10,000 participants," Grun says proudly. "Our vision is to be a global company that changes the world and sells better quality, healthier plant-based dairy alternatives. Our factory is located in Netivot and we are proud to contribute to the city and to provide jobs for families in Israel's geographical periphery. We regard this as the epitome of Zionism."
The article was written in collaboration with the Israel Innovation Authority, responsible for the country’s innovation policy. Its role is to nurture and develop Israeli innovation resources, while creating and strengthening the infrastructure and framework needed to support the entire knowledge industry.
Part One: The Cutting Edge: Manufacturing using advanced technologies
Part Two: A fast-track to innovation: The R&D Preparatory Incentive Program
Part Three: Innovation in the aftermath of Covid-19: necessity is the mother of invention
Part Four: Smart industry and advanced mechanization: a technological leap forward to the global market