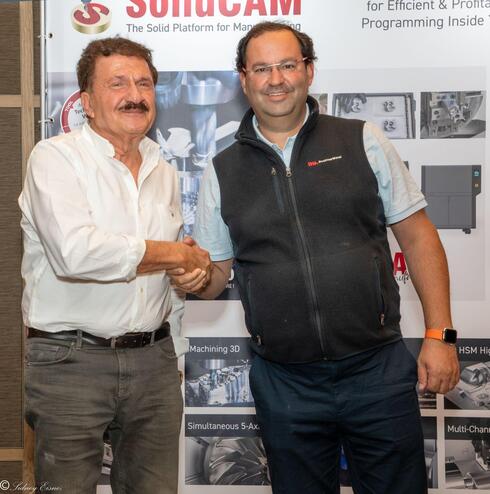
CAM software leader SolidCAM, launches its Metal 3D printing business
SolidCAM, the leading CAM software for CNC manufacturing, launches its metal 3D printing business worldwide
The global partnership between SolidCAM and Desktop Metal enables SolidCAM to provide Desktop Metal systems to its SolidCAM customers around the world, with the target to manufacture metal parts in a faster, more efficient, and more profitable process. 3D printed parts have already been integrated into a variety of industries worldwide, from cars to medical products.
3D printing of metal parts is a major feature in the future of industrial production
In recent years, major manufacturers have shown a growing interest in the 3D printing of parts. One of the key industries that benefited from 3D printing is the defense industry, which was one of the first to adopt these advanced manufacturing technologies, and also the electrical vehicle industry, where many of the internal components are designed and manufactured leveraging 3D printing technologies. Other industries such as aviation, aerospace, and medical products, use 3D printed metal parts to reduce the weight of products, customize parts, and reduce costs. Overall, 3D printing can optimize the design and manufacturing processes across a multitude of industries.
SolidCAM joins now the 3D Printing up-and-coming market. SolidCAM is one of the world leaders in the field of CAM software for CNC manufacturing, serving customers ranging from Toyota, Honda, Hyundai, Volkswagen and Skoda to technology companies such as Intel, HP, Facebook, Amazon, Panasonic, Nikon and Canon, to aerospace companies Airbus and SpaceX, to defense industry companies such as Elbit, and Rafael, to consumer goods giants such as Procter & Gamble, Bosch and Michelin Tires.
SolidCAM’s target is to be the worldwide leader in combining metal 3D printing with CNC machining. Dr. Emil Somekh, founder and CEO of SolidCAM, says that: "Today there are over 20,000 CNC workshops and manufacturing companies in the world that use SolidCAM’s software solutions. We have asked ourselves how we could move forward and innovate, and we identified Metal 3D printing technology as the ideal complement to the CNC manufacturing processes.”
SolidCAM then initiated its strategic collaboration with Desktop Metal, the world's leading company in 3D printing of metals. The collaboration makes it possible to combine, for the first time, the two manufacturing methods, that until now were conducted separately - Additive and Subtractive. Dr. Somekh explains: "Additive manufacturing comes to complement CNC manufacturing, which operates on the Subtractive principle. Thanks to these complementary technologies, it will be possible to manufacture sophisticated and complex products which, until today, could not be produced using existing manufacturing methods." 3D Printing is used for Rapid prototyping, part consolidation, complex geometries, design customization, rapid tooling, on-demand manufacturing and supply chain re-engineering.
Enjoy the best of both worlds – Metal 3D Printing combined with CNC machining
To better understand the principles of these two manufacturing methods, let’s look into these processes and their differences. Subtractive Manufacturing in CNC Machining is the act of removing material by milling, turning, or drilling. In contrast, Additive Manufacturing uses the innovative 3D printing technology, that adds layers of stock material on top of pre-existing layers, to create the three-dimensional part.
Metal parts that have been 3D printed, often need postprocessing, using CNC machining to finish locating surfaces, tight tolerance features and drilling holes. Therefore, it was a natural move for a company like SolidCAM, which has a deep understanding of the CNC machining field, to aim to be the market leader in consulting, training and implementation of metal 3D printing, combined with CNC manufacturing. Digital control of the 3D printing process enables dynamic changes to be made in the product components, saving significant time and production costs.
2 View gallery
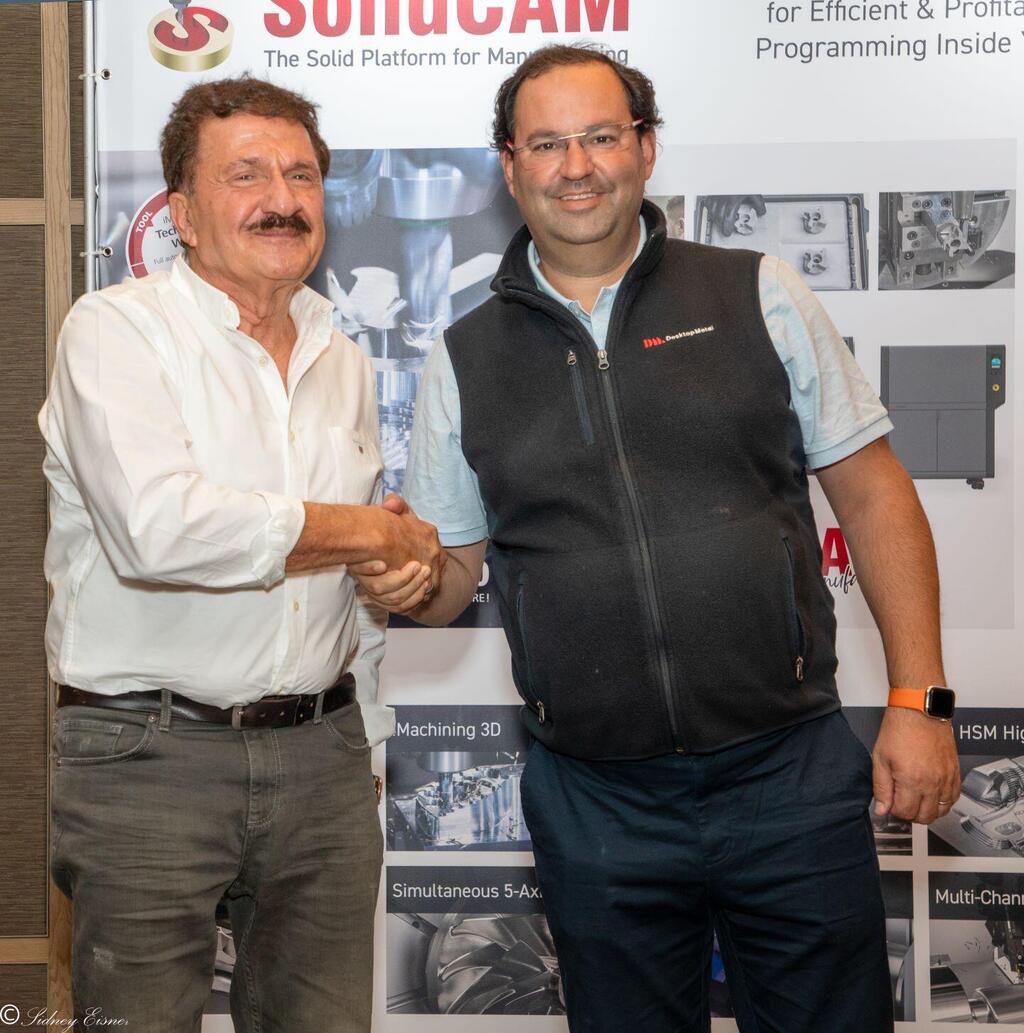
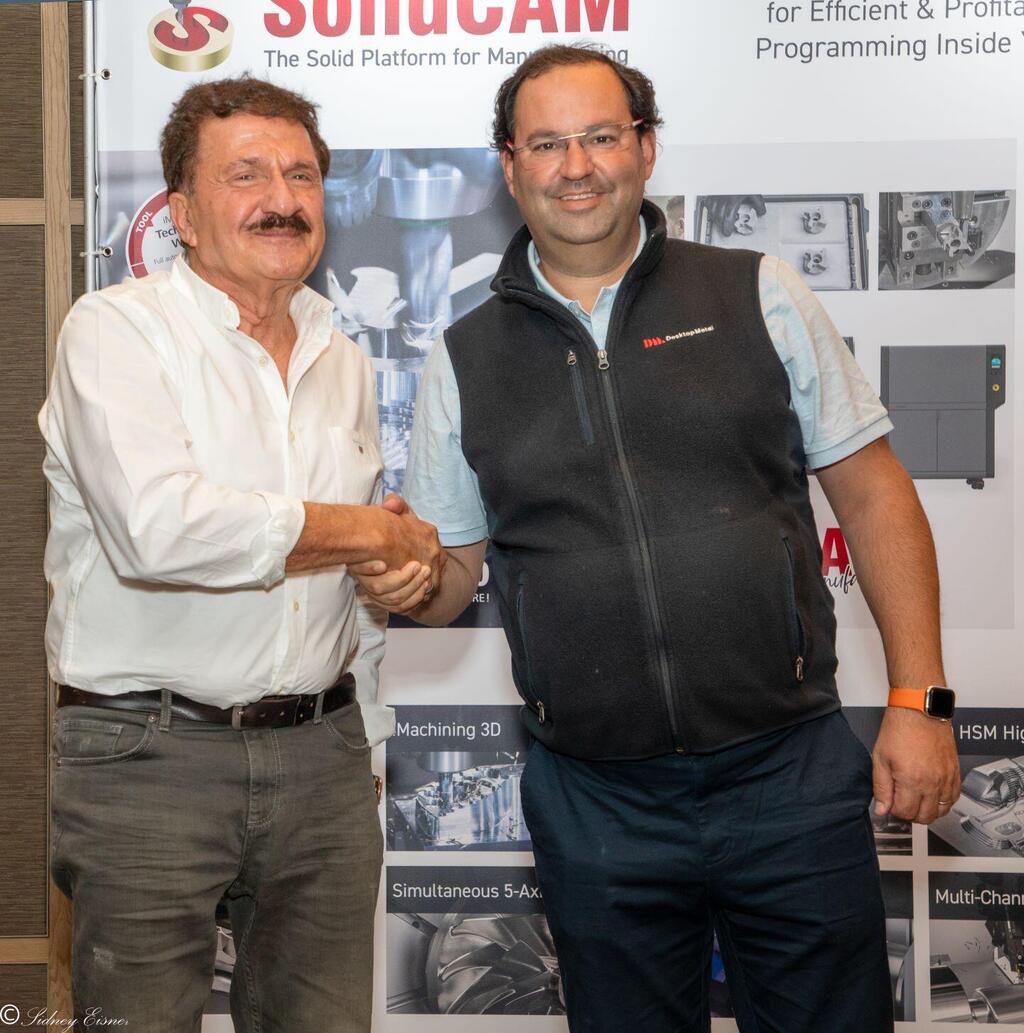
Dr. Emil Somekh (left), founder and CEO of SolidCAM, and Ric Fulop, founder and CEO of Desktop Metal, at the SolidCAM conference that was hosted in Tel Aviv this past October
(SolidCAM)
A powerful collaboration between two tech leaders
Last October, SolidCAM announced its partnership with Desktop Metal in front of 250 representatives from SolidCAM branches and resellers around the world, at its SolidCAM Worldwide 2022 Reseller conference, at the Hilton Hotel in Tel Aviv. Ric Fulop, founder, and CEO of Desktop Metal, who presented at the conference, said: "The worldwide collaboration between Desktop Metal and SolidCAM will enable many customers to take advantage of the tremendous potential inherent in combining metal 3D printing with advanced CNC methods, to optimize their manufacturing processes, and open up opportunities for new lines of products, that could not be manufactured until today.”
Desktop Metal offers two leading metal 3D printers for the industry. The Studio 2 system is used to print metal prototypes and small series of end-use metal parts, using the Bound Metal Deposition (BMD) process. The Shop System introduces high quality binder jetting for an entirely new market of machine shops - shops can now cost effectively 3D print end-use metal parts, with unparalleled speed and productivity, with superior surface finish and resolution versus laser-based 3D printing systems, at a fraction of the cost.
2 View gallery
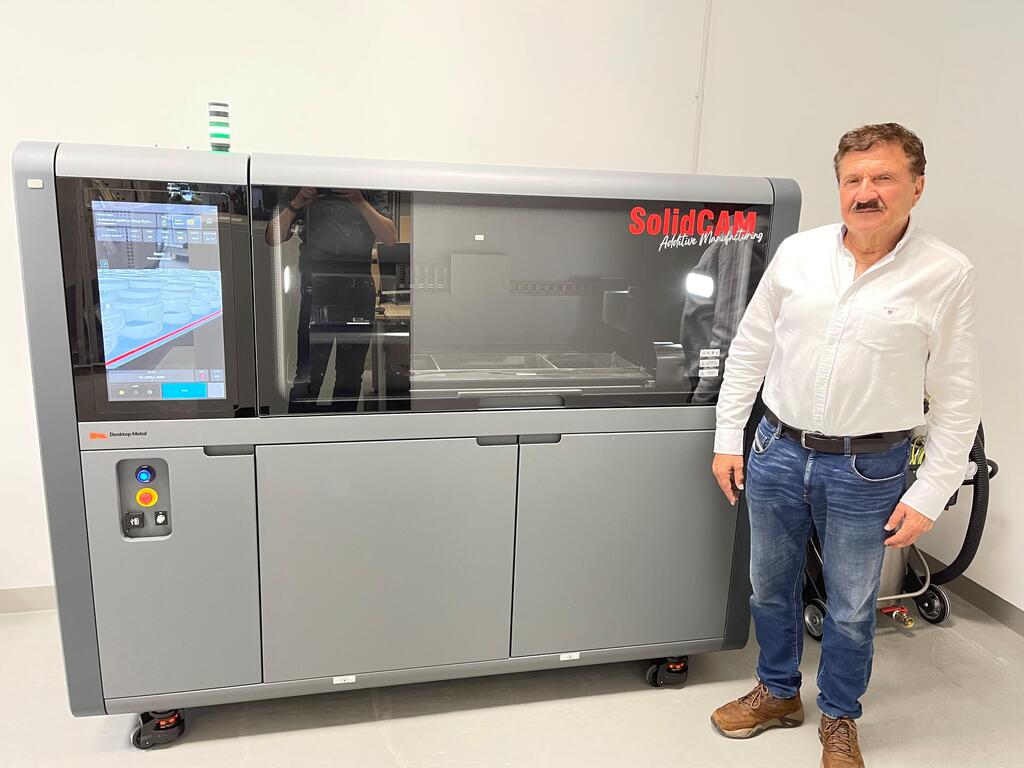
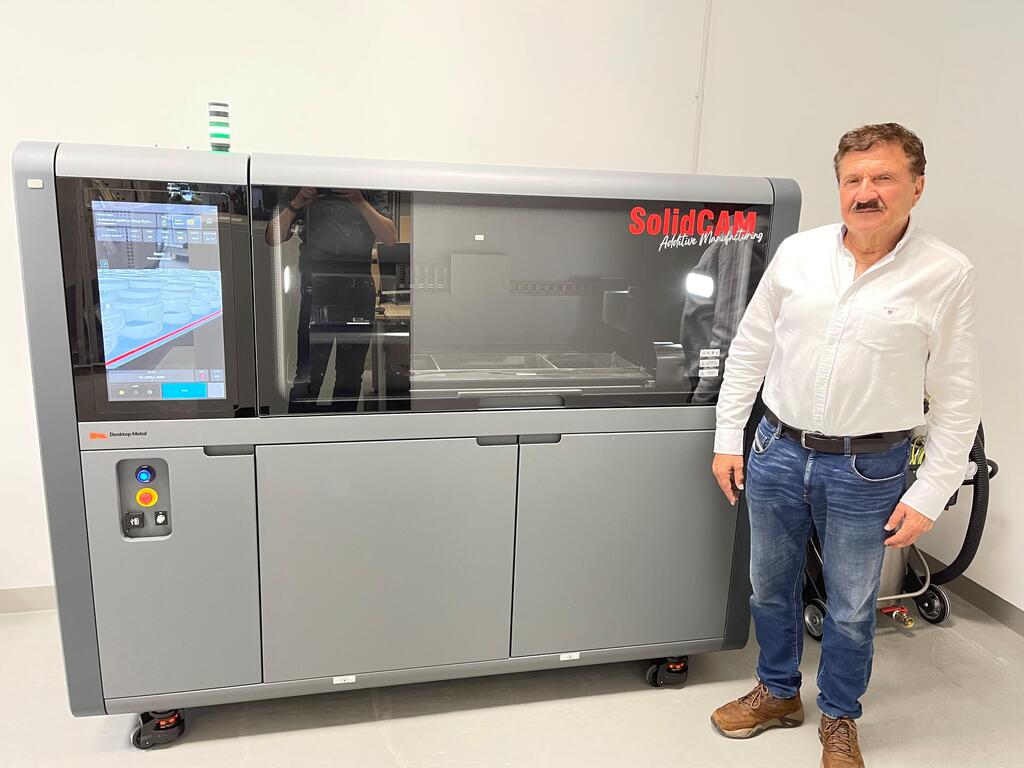
Dr. Emil Somekh stands next to a Desktop Metal Shop system, at the SolidCAM technology center in Germany
(SolidCAM)
Following the cooperation between the two companies, the Desktop Metal 3D printing systems will be marketed and sold to SolidCAM customers, through the company's branches and resellers worldwide, in Europe, USA and APAC. Technology centers in Germany, USA, and Israel will enable SolidCAM customers to check the capabilities of the 3D printers on their relevant parts. Dr. Somekh elaborates: "We have established technological centers in various countries in the world for the study, research and demonstration of Metal 3D printing, and we are ready to offer our customers comprehensive consultation and training in the combined process of metal 3D printing and CNC, including providing full technical support for the manufacturing processes of the new 3D printers."
First published: 16:19, 03.01.23