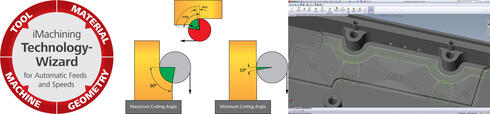
SolidCAM iMachining - the CAM technology that is revolutionizing the CNC industry!
The largest manufacturers in the world, from aerospace to automotive to tens of thousands of smaller manufacturers and machine shops, use SolidCAM’s patented iMachining technology in CNC machining. This innovative technology reduces machining cycle time by 70% and more and extends the cutting tools’ life five times and more. SolidCAM is a leading worldwide leader in CAM software for CNC machining.
(Channel Mill-Turn milling using iMachining technologies)
SolidCAM’s iMachining is the top innovative technology in the CNC machining industry. This unique patented technology dramatically improves the productivity of CNC manufacturing processes, saving time, and cutting costs, and has been adopted worldwide by companies who utilize CNC machines in manufacturing - these include technological giants such as HP and Intel, Aerospace manufacturers like SpaceX and Airbus, car manufacturers like Volkswagen, Honda and Skoda, leaders in the defense industry like Raphael and Elbit, Boston Scientific in the medical sector, and other companies including M3, Bosch, Yamaha, Facebook, Amazon and many more.
Dr. Emil Somekh, founder, and CEO of SolidCAM, explains:
"In a competitive market, the name of the game is increased productivity. It is very important today for CNC machine shops to manufacture as quickly as possible, while reducing expenses, increasing productivity, and extending the lifespan of their CNC machines. Of the 20,000 customers of SolidCAM worldwide, most are already using the iMachining technology, for which we’ve already registered 7 exclusive patents. We offer iMachining 2D, for prismatic parts, and iMachining 3D for 3D complex parts. Both of these technologies optimize the manufacturing processes by dramatically saving CNC machining time and cutting tools expenses."
The most advanced technology for saving machining time and manufacturing costs.
iMachining’s revolutionary technology makes it a “game changer” in the CNC machining industry. This is especially true for the iMachining Technology Wizard, which automatically calculates the optimal feeds and speeds for the cutting tools on the CNC machines. These calculations are carried out according to the properties of the stock material being cut, the type of cutting tool and the parameters of the CNC machine. Without the iMachining Wizard, it would be necessary to weigh all these properties and parameters manually, requiring a lot of guesswork and trial & error work, even among experienced CNC programmers. The Wizard’s addition, to the convenient and easy to learn and use interface of the SolidCAM software, dramatically enhances the work of the CAM programmers.
Another exciting iMachining element is the Intelligent Tool Path Generator, which calculates an optimal morphed spiral toolpath for machining, minimizing also the air cutting time. When there are features that must not be machined, a trochoidal tool path is generated around them.
When using the iMachining technology, a part that once took 17 minutes to machine can be completed in only 6 minutes. With aluminum parts you can save up to 70% in machining time, and with titanium and steel parts you can save 80% in machining time. This technology also extends dramatically the lifespan of the cutting tools by 5 times and more.
Avi Tagar, owner of the Mecanodin CNC machine shop and veteran SolidCAM user, says that:
"iMachining 3D is a unique technology that is light years ahead of what others offer in the CAM market today. We currently implement iMachining in most of our CAM programs. Thanks to the SolidCAM software, and especially thanks to iMachining 3D, we’ve saved an unbelievable amount of machining time and have tremendously extended the life of our cutting tools.”
1 View gallery
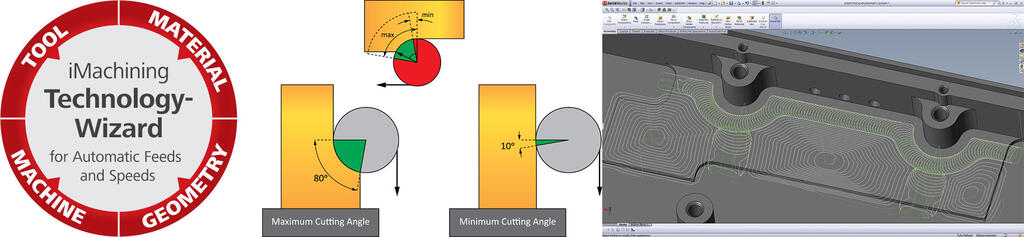
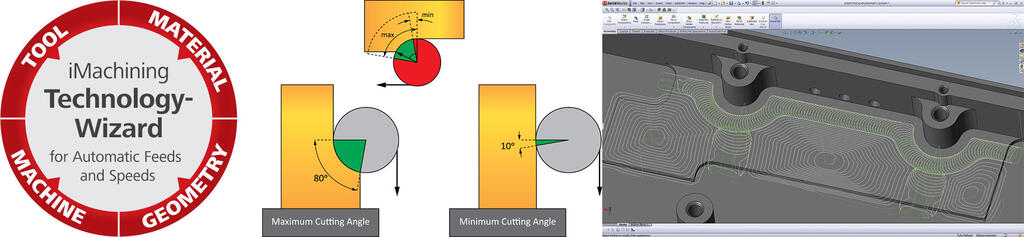
iMachining demonstrates a spiral morph track using variable cutting speed according to the cutting angle, which is control by the WIZARD
(solidcam)
Machine Shops reduce operating expenses and preserve the life of their CNC machines
The reasons more and more manufacturers are switching to iMachining is that it reduces machining time, extends cutting tool life and optimizes the maintenance of the CNC machines used. During iMachining cutting, the tool is in contact with the material at different cutting angles and with varying feeds - at a large cutting angle the feed is automatically reduced, and at a small angle the feed is increased. The result is that iMachining guarantees a constant load on the cutting tool.
Dr. Somekh explains that "iMachining dynamically controls the feed and spindle speed of the operations and keeps the cutting angles between 10 and 80 degrees. When the Spindle load remains stable at 20% in this process, the chips produced are the same size throughout, preserving uniformity in the operation of the CNC machine and the highest work efficiency."
Another important factor in machining efficiency is the depth of cut. In regular cutting, usually only the bottom portion of the tool is used for cutting, and the wear is only at the end portion of the tool. iMachining makes it possible to machine the material at the full depth of the cutting tool, so the load is distributed evenly along the length of the tool and the wear is uniform. This minimizes machining time and cutting tool costs for manufacturers.
Yariv Peer, owner of A. Peer Industries and SolidCAM client says:
“We use iMachining for daily work because of the value the module adds in terms of saving manufacturing time, extending the cutting tools life and preserving the life of the CNC machine. With iMachining, we know that our CAM programmers are using precise, scientific, and proven technology, with optimal cutting conditions.”
(Pattern milling using iMachining 3D technology )
How iMachining started, and where it is going!
In 2006, Dr. Somekh’s student daughter, Natalie, was looking for a job as a waitress. She interviewed at a restaurant whose owner, as it turns out, previously knew her father through previous work. When Natalie told him of her interview, Dr. Somekh went to visit the restaurant accompanied by the senior programmer at SolidCAM. There, over a plate of hummus, Somekh convinced the owner of the restaurant to return to work in CAM, thanks to his rich experience in the field, and to assist in developing a morphed spiral milling path. The initial sketch of the toolpath shape was done by Somekh on a paper napkin at the restaurant, and 3 years later the iMachining technology was launched, completely changing the world of CNC machining and the future of SolidCAM.
Today, the SolidCAM software is involved in the manufacturing of a large number of products in the market. SolidCAM employs 280 staff worldwide, sells through branches and resellers in over 70 countries, and operates technological centers in Germany, USA and many other countries for CNC machining R&D, prospect customers benchmarks, and training for CAM programmers and Operators on the optimal ways of CNC machining.
Dr. Somekh concludes:
"Year after year, SolidCAM continues to improve, innovate and dictate the direction in which the CNC machining toolpath technology is progressing. Now we are developing an innovative technology, called iTurning, which will leverage the main concepts of the iMachining milling technology to enhance the toolpath of the lathe turning operations, giving an additional major advantage for CNC manufacturers worldwide.”