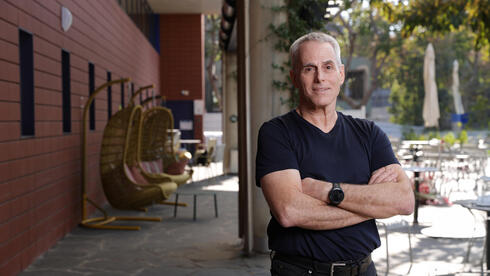
Semiconductor giant bets on Israel despite challenges
Rafi Benami explains why Applied Materials is investing in its largest R&D hub outside the U.S.
At the entrance to the office of Rafi Benami, General Manager of Applied Materials Israel, are landscape photos of Alaska, New Zealand, and Mount Kilimanjaro—captured during his travels around the world. One of the photos shows four feet wearing hiking boots on a mountain peak in the White Mountains National Park in New Hampshire, symbolizing the long journey he and his son took together. Another photo offers a breathtaking view from the Milford Track in New Zealand, taken during a post-army trip with his daughter. This theme—the journey—is both a life philosophy and a management approach for Benami. His personal journey to leading an organization of 2,000 employees in Israel, which has doubled its size in the past three years under his leadership, began 12 years ago.
Applied Materials is a public company employing tens of thousands globally, specializing in chip manufacturing processes. The Israeli branch focuses on machinery and quality control products for chip production and is the company’s largest R&D and manufacturing center outside the U.S. Benami assumed the General Manager role in early 2022, during the twilight of the high-tech boom, only to be thrust into a global crisis, alongside Israel’s judicial reform turmoil and a prolonged war that has lasted over a year.
You took office during the peak of growth in Israeli high-tech, and now everything is different. How have you experienced these three turbulent years?
"There is the storm in Israel that we are dealing with as managers in a challenging environment. However, our business is shaped by the semiconductor industry's global state, which is at the heart of global technology. The demand for chips—for AI, cars, data processing, and memory—is only increasing. As a company, we expect demand in the semiconductor industry to grow by 50% by 2030, so we’re operating in an environment with a very optimistic forecast.
"Additionally, Applied Global has significantly increased its investment in us. Since 2021, we have nearly doubled our workforce and financial investments in the Israeli branch. We now have a campus with three buildings, and we’re constructing a fourth as part of this expansion. This growth reflects our confidence in the industry’s direction and the company’s future. From a business perspective, I am very optimistic about where we’re heading. On the national level, however, the challenges are immense."
On October 7, Benami drove his son, who serves in an elite unit, to the army and then convened the company’s business continuity forum to implement contingency plans for uninterrupted operations. The war has deeply impacted the company. Applied Israel lost four employees, including Yehuda Cohen, a veteran employee whose son, Nimrod Cohen, was kidnapped and taken to Gaza. Since the war began, 15% of the company’s workforce has been drafted into reserve duty, with up to 300 employees serving simultaneously. To address the labor shortage, Applied Materials Israel reached out to retired employees, asking them to return temporarily, and expanded its facilities.
The company rented an entire hotel in Rehovot’s industrial zone to house families of employees from areas affected by the war, including the Gaza border region. It provided financial aid to families whose homes were damaged and offered psychological support to employees grappling with the traumatic events.
Do you think global management at Applied Materials might eventually lose patience with the situation in Israel?
"The bottom line is no. Applied Materials has been heavily invested in Israel for many years, and I’ve managed to convince the CEO to increase that investment further. Since October 7, we’ve proven to both management and customers that we can operate effectively in these challenging circumstances. Despite initial concerns, we’ve continued delivering machines and support to customers without interruption.
"Our global management, based in Santa Clara, California, moved from a place of concern to confidence as they saw us maintaining operations seamlessly. One key reason is that even before October 7, we built our operations as a global company. We have a strong core in Israel, complemented by robust teams in India, Germany, and near our customers. This global balance enables us to maintain business continuity even in difficult times."
So, has some of the activity shifted abroad?
"We haven’t moved operations abroad—we’ve diversified them. This global diversification allows us to mitigate risks. That said, we continue to recruit locally, with over 80 open positions in Israel spanning technology fields like physics, software, and algorithms. Globally, we’re hiring for a similar number of roles. This balance, paired with building a strong core here in Israel, is why we’ve been able to navigate this challenging environment successfully."
Benami lives in Ramat Gan with his wife, Professor Orly Sade, Dean of the Faculty of Business Administration at the Hebrew University, and their two children. His journey at Applied Materials began over a decade ago, following roles at global tech firms like Comverse and NICE. Reflecting on his early days at the company, Benami admits it wasn’t "love at first sight."
You said it’s a difficult company to integrate into. Why is that?
"This stems from the complexity of our work. We deal with a wide range of technologies, each requiring deep expertise. These technologies must be integrated while meeting specific customer needs. To succeed here, you need a passion for learning and a commitment to staying up-to-date. Transitioning from NICE, a software company, I had to dive deeply into entirely new technologies—it was a challenge."
Throughout your career, you’ve climbed the corporate ladder. Do you have tips for succeeding in large organizations?
"First, you need to excel in your work, but that’s not enough. Collaboration is key—you can’t achieve anything alone. You’re only as good as your partners, so you must foster win-win collaborations. Also, balancing a broad systems perspective with the ability to dive into details when needed is critical. This combination drives large organizations forward."
Are you working in a hybrid model? Does it make collaboration harder?
"Since the pandemic, we’ve adopted a hybrid model of two to three days in the office. While hybrid work has its benefits, interpersonal interaction is irreplaceable. That’s why we’re building a new office, opening in October, to encourage employees to return. Long-standing relationships built here over the years have helped us maintain collaboration, even in a hybrid setup. But eventually, some of the intangible benefits of working together in-person will be lost."
Applied Materials Israel’s offices feel more like an industrial plant than a typical Israeli high-tech workspace. The company produces physical products, unlike many software-focused firms, even as it operates at the forefront of chip technology.
How does the current high-tech job market affect your company?
"Fortunately, we’ve remained an attractive workplace, even during the high-demand years of 2021–2022. Today, it’s easier to recruit, but we’ve always maintained diversity in hiring, bringing in both juniors and experienced professionals. This approach creates a healthier, more innovative organization."
What are your predictions for Israeli high-tech in 2025?
"The current situation in Israel is harming Israeli high-tech. For it to thrive, we need stability—people and capital must flow freely in and out of the country. Unfortunately, Israel’s ‘brand’ is being damaged. Social cohesion and shared values are critical for high-tech success, and right now, those are under threat.
"At Applied Israel, we’ve succeeded because we’ve built a strong core of values that fosters acceptance and collaboration. This foundation allows us to build a healthy, productive company, and it’s something Israel as a whole urgently needs to reclaim."